Issue in number range missing
I was facing the issue of missing numbers in the number range for one of my object. I had tried many solutions but not succeed. Then I have found one solution for this issue. I am just sharing the solution with you.
In SNRO, if you will check the field ‘No. of Number in buffer’ as highlighted.
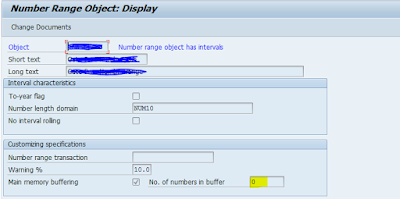
This number determines how many numbers are reserved in the application server buffer for the intervals.
Earlier this filed was 10, so each time, 10 numbers were reserved in the application server buffer for the intervals and due to this reason numbers were missing. Now I have set it as 0. After this my problem has been resolved.
Please do the same as per following screen shots.
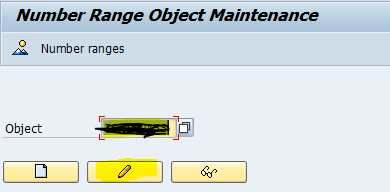
Click on
to change and then change the value as highlighted.
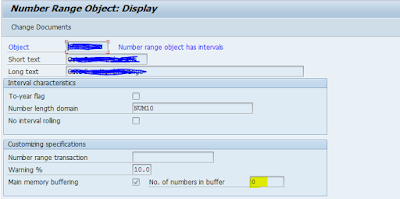
After this change, no number will be missing from the number range.
I was facing the issue of missing numbers in the number range for one of my object. I had tried many solutions but not succeed. Then I have found one solution for this issue. I am just sharing the solution with you.
In SNRO, if you will check the field ‘No. of Number in buffer’ as highlighted.
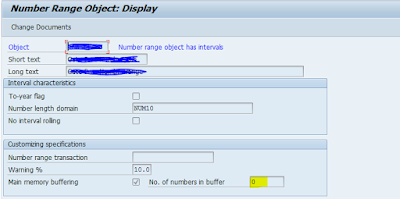
This number determines how many numbers are reserved in the application server buffer for the intervals.
Earlier this filed was 10, so each time, 10 numbers were reserved in the application server buffer for the intervals and due to this reason numbers were missing. Now I have set it as 0. After this my problem has been resolved.
Please do the same as per following screen shots.
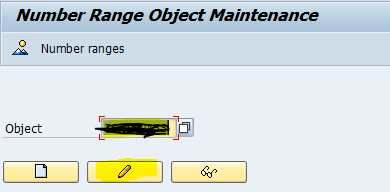
Click on

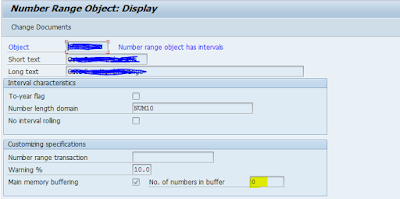
After this change, no number will be missing from the number range.